Get the latest news from tracezilla
9 updates in July including update of forecasting and delivery overview
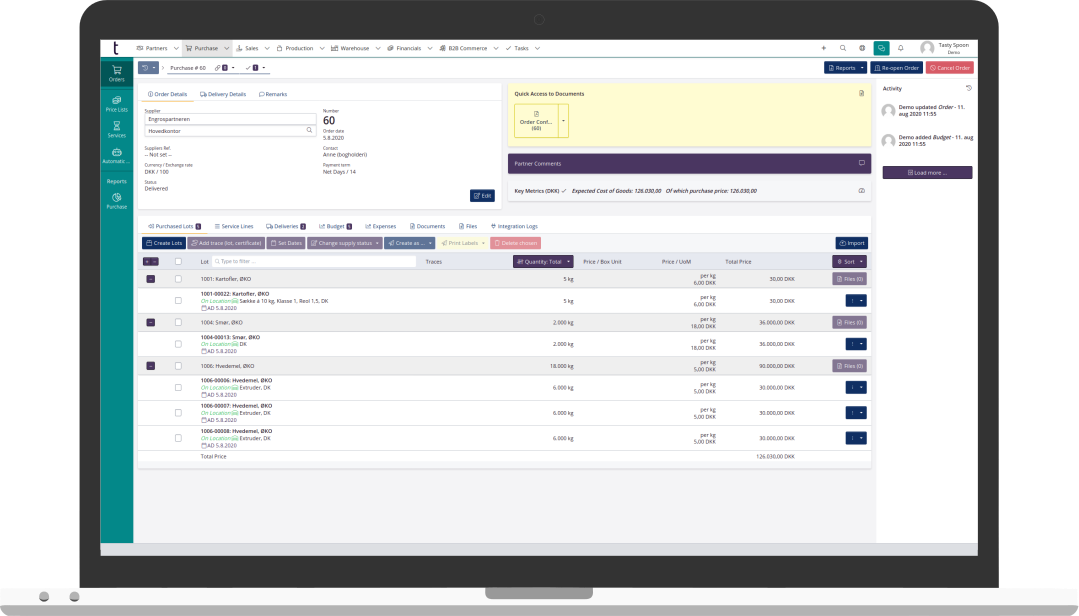
Improved delivery overview and quick addition of lot information
The delivery page in tracezilla is an ideal tool for the warehouse employee, who does not work directly with purchasing and sales, but who is responsible for receiving goods and sending goods.
In July, exciting things have happened on the delivery page. It has been updated with the following:
- New delivery status for incoming deliveries: Arrived.
- Batch number and dates can be added directly from the delivery page.
- The overview has become simpler and more user-friendly.
Read more about Deliveries.
Plan production and estimate consumption of raw materials
tracezilla’s forecasting has been updated with two valuable features.
1) In the forecasting you can enter your expected supply, ie. how much you plan to produce of a given product. Now you can create production orders directly from the forecasting with the quantity you entered as expected supply. It makes it easier for you to plan to produce to stock (MTS).
2) The forecasting tool has for a long time been able to estimate the consumption of semi-finished products, raw materials and packaging for production for each part of the process chain. Now tracezilla can estimate the consumption for production from the finished product and all the way down to the individual raw material in one click, even though there are several process steps.
In addition, the forecasting function now starts on the supply page, except for users with the salesperson role. In this case, the function starts on the sales forecast.
Explore our forecasting feature here.
Pass expiry date from raw material to finished product automatically
In tracezilla you can create a recipe that indicates which semi-finished products, raw materials and packaging are used in the production of a finished product.
The recipes serve many purposes, including documentation in mass balances for certified goods, advanced cost calculation and quick and easy creation of production orders.
Now you can also set up tracezilla to pass on the expiration date from a raw material to the finished product using recipes. The function is useful when the shelf life of your end product depends on the raw material in the specific production that has the shortest shelf life.
Read more about recipes here.
Set the relevant expiry date type for your product
You can specify a best before date or an use by date on your products in tracezilla. Since there is a difference in meaning of the two date types, a new setting has been added to SKUs (stock keeping units).
You can now set which of the two date types is the correct one for a given product. When receiving goods in a purchase order or a production order, only one field will appear.
With the setting, you can ensure that it is the correct type of date information that is passed on to your customers regarding shelf life.
Read more about the creation and configuration of SKUs here.
Enter the posting date of the vendor invoice on the purchase order
Should the cost prices of your goods only be included in the inventory value after posting the invoice from the supplier? Then we have good news for you.
You can now enter the posting date on the purchase order - without having enabled the extension Actual Cost Pricing.
Now there is a field to enter the posting date of the invoice. The field is located in the order header of a received purchase order. Thereby, tracezilla will use this date rather than the delivery date, when inventory value is calculated on the basis of the cost price of the goods received.
Actual cost pricing is included in the subscriptions Trade, Manufacturing and Bundle. Enable it for free in the extensions if your subscription plan is one of the above.
Using actual cost price calculation, your posted expenses are matched to purchase orders and lots. Your cost prices and thereby also your inventory value will be calculated on the basis of realized costs.
Read more about the calculation of cost prices in tracezilla.
Read more about purchase orders in the tutorial.
Get insight into changes with the activity log for stock keeping units
When working together to update data and add orders in a system, it may be relevant to see changes and when the changes have been made. In tracezilla there is an activity log which shows this on orders, partners, lots and more.
Now the activity log is also added to SKUs. You can see when a SKU has been edited and what has changed in the setup.
Read more about the creation and configuration of SKUs here.
Select the relevant lot attributes for your company
You can add information to your SKUs, which can vary from lot to lot. These informations are called attributes.
For example, you can enable the attribute Storage bin to indicate where a given SKU is typically located in the warehouse, e.g. “Shelf A2”. When receiving supplies, there may not be room for the goods at the usual location. You can therefore change the location of the individual lot so that employees in the warehouse knows where the goods are to be picked from.
In your company settings, you can, as something new, choose the attributes that are relevant for your products. This limits the options in the SKU settings, which gives you a better overview.
You can activate the attributes and set a default value for each SKU, and change the information for each lot.
Font size, bold font and update of document settings
The font size and font weight are now divided into two settings. In addition, you can select fixed width as the font type so that the order lines on documents can be read by machines.
Bank account details are located on a separate tab now.
Read more about the document settings.
Update of the order settings
Three new order settings have been added.
For outbound lot lines, you can select whether there should be a box to tick so that the inventory status of a lot can be adjusted automatically to 0 or whether the quantity picked for an order may be adjusted during the selection of lots that are picked from the warehouse.
In addition, there is an option to choose which invoice date should appear automatically when invoicing a sales order, e.g. todays date, date of risk transfer, etc.
Read more about the order settings.
Receive our newsletter
